Imagine the all-too-familiar scenario: you reach into a drawer brimming with charging cables, each tangled with the next, and none seem to have the right connector or length for the device in your hand. It’s a small frustration of modern life, a minor annoyance we’ve all experienced. But this simple example touches on a fundamental need in the world of electronics – the right connections matter. While we might only think about these everyday cables, the need for precise and reliable connections extends far beyond our personal devices. In countless industries and applications, having the correct cabling is not just a matter of convenience, but a necessity for performance, safety, and efficiency. This is where the concept of cable assemblies comes into play, offering a way to bring order and functionality to the complex world of electronic connections.
What’s the Deal with Cable Assemblies Anyway?
At its core, a cable assembly, which you might also hear referred to as a cable harness or wiring loom, is essentially a carefully organized group of multiple wires or cables that are bound together into a single, manageable unit. This bundling is often achieved using a protective outer layer made of materials like rubber, vinyl, or thermoplastic, or even with simpler methods like cable ties and tapes. Think of it as taking a collection of individual strands and weaving them together to create a strong and unified cord. This structured approach makes these groups of cables significantly easier to install, replace, and maintain in a wide range of electrical and electronic systems, from the simplest household gadgets to the most intricate industrial machinery. Instead of dealing with a jumble of individual wires that can easily become tangled and confusing, a cable assembly presents a clean and organized solution. Beyond just tidiness, this bundling also plays a crucial role in protecting the internal wires from environmental factors and the general wear and tear that can occur over time. The primary function of these organized bundles is to efficiently and safely transmit electrical power, data, or signals between different components or devices within a system. They act as the essential lifelines that allow our electronics to communicate and perform their intended tasks.
Off-the-Shelf Cables: Convenient, But Are They Always the Answer?
For many common needs, the market offers a wide array of off-the-shelf (OTS) cable assemblies. These are pre-fabricated, ready-made cables and wiring harnesses designed to suit a broad spectrum of standard applications. Their most significant advantages lie in their lower cost, thanks to mass production, and their immediate availability, as they are typically stocked in warehouses and readily accessible for purchase. You can find them in standard lengths and configurations, equipped with common connector types such as USB, HDMI, Ethernet cables for internet connections, and power cords for plugging into outlets. These readily available options are often ideal for prototyping new electronic projects, handling basic connectivity needs, and fulfilling general applications where highly specific requirements for length, materials, or connectors are not a major concern. Due to the large-scale production involved in creating these standard cables, the cost per unit is generally lower compared to solutions that are custom-made. For instance, you can find various Molex off-the-shelf cables ranging in price from under a couple of dollars to around twenty dollars, depending on the type and length. While these standard options offer convenience and affordability for many situations, their “one-size-fits-all” nature means they might not always be the perfect solution for every unique need. It’s worth noting that even within the realm of off-the-shelf cables, there can be some variation in terms of color and length , offering a degree of choice for standard applications. Furthermore, these cables are often manufactured to meet established industry standards, and they come with compliance certifications, providing a level of quality assurance for typical uses.
Custom Cable Assemblies: Getting Exactly What You Need (and Why It Matters)
In contrast to the standardized nature of off-the-shelf options, custom cable assemblies are designed and manufactured to meet the precise and unique specifications of a particular project or application. This means that virtually every aspect of the cable assembly can be tailored to your exact requirements. This customization can involve specifying the exact length of the cable needed, choosing specific types of connectors to ensure perfect compatibility with your equipment, and selecting the most suitable materials for the inner insulation, the protective outer shielding, and the outermost jacket, all based on the specific environment and performance demands of the application. Beyond these fundamental aspects, customization can also extend to more detailed features such as color-coding individual wires within the assembly for easy identification, adding labels for quick reference, and even integrating multiple types of cables – for example, power, signal, and video – into a single, unified assembly. The process of creating a custom cable assembly often involves a close and collaborative relationship between the customer and the cable assembly manufacturer. This partnership ensures that all the specific needs of the project are thoroughly understood and meticulously addressed, taking into account factors like the required electrical load, the environmental conditions where the assembly will operate, and any other specific functionalities that are needed. A particularly significant aspect of custom cable assemblies is the ability to select specific materials that are best suited to withstand particular challenges, such as extreme temperatures, exposure to chemicals, or the presence of electromagnetic interference (EMI). Furthermore, the use of advanced techniques like 3D modeling and virtual manufacturing in the custom cable assembly process highlights the level of precision and pre-production validation involved, which is not typically a feature of standard off-the-shelf options.
The Perks of Going Bespoke: Why Choose Custom Cable Assemblies?
Opting for a custom cable assembly offers a range of compelling advantages, particularly when the application has specific or demanding requirements. One key benefit is optimized performance. By designing the cable assembly with the specific electrical needs of the application in mind, manufacturers can ensure efficient power and signal transmission, minimizing potential issues such as voltage drops or signal interference. It’s akin to having the right-sized pipes for your electricity and data, ensuring everything flows smoothly without bottlenecks. Another significant advantage is the perfect fit. By specifying the exact length and the precise connector types needed, custom assemblies eliminate the clutter and inefficiency of excess cabling, ensuring seamless integration with the equipment and reducing the risk of incorrect connections. Think of it as eliminating messy cable nests behind your devices. Enhanced durability is another major perk. Custom cables can be constructed using high-quality, application-specific materials that are designed to withstand harsh environments, extreme temperatures, vibrations, and exposure to chemicals, leading to a longer lifespan for the assembly and reduced downtime for the equipment it serves. Furthermore, improved efficiency in installation, maintenance, and troubleshooting can be achieved with custom assemblies due to the streamlined cable management they offer. When everything is organized and fits perfectly, setting up and resolving issues becomes a much faster and simpler process. Finally, while the initial investment in a custom cable assembly might be higher compared to an off-the-shelf option, there can be reduced waste and long-term cost savings. By ordering the exact amount of cable and using only the necessary materials, custom solutions minimize waste. The increased performance, enhanced durability, and reduced need for maintenance and replacements can contribute to overall cost savings over the lifespan of the equipment. The stringent quality assurance and rigorous testing that custom cable assemblies often undergo provide a significant advantage in terms of reliability compared to off-the-shelf options where the manufacturing process might be less transparent. Additionally, the ability to incorporate specific features like shielding against electromagnetic interference (EMI) in custom cables is crucial for sensitive equipment and environments with electrical noise, a benefit that is not always standard in off-the-shelf options.
Here’s a table summarizing the key differences:
Feature | Off-the-Shelf Cables | Custom Cable Assemblies |
Cost | Generally lower upfront cost | Potentially higher upfront cost, but can be cost-effective long-term |
Availability | Readily available, immediate delivery | Requires manufacturing time |
Customization | Limited to standard options (length, basic connectors) | Highly customizable (length, connectors, materials, etc.) |
Performance | Suitable for standard applications | Optimized for specific application requirements |
Fit | May not be a perfect fit for specific setups | Exact fit, eliminates excess cable |
Durability | Designed for general use | Can be designed for specific environmental conditions |
Waste | Potential for excess cable and unused features | Minimal waste, exact quantities used |
Complexity | Simple, standard designs | Can accommodate complex designs and multiple functions |
Long-Term Value | May need more frequent replacement in demanding apps | Higher reliability and lifespan in appropriate applications |
Where Custom Cables Really Shine: Real-World Scenarios
There are numerous real-world applications where the benefits of custom cable assemblies make them the clear choice over their off-the-shelf counterparts. In the medical industry, for example, custom cable assemblies are essential for medical devices that require the ability to withstand rigorous sterilization processes, must be biocompatible to ensure patient safety, and need to provide reliable signal transmission for critical applications like patient monitoring systems and medical imaging equipment. The automotive industry also heavily relies on custom cable assemblies to connect the vast array of sensors, control units, and power systems within modern vehicles, demanding exceptional durability against constant vibrations, extreme temperature fluctuations, and exposure to moisture and chemicals. In the demanding fields of aerospace and defense, custom cables are paramount for ensuring reliable communication, precise navigation, and consistent power transmission in aircraft, satellites, and military equipment, where they must perform flawlessly under extreme conditions where any failure could have catastrophic consequences. Industrial automation and manufacturing facilities utilize custom cables that are specifically designed to resist harsh chemicals, withstand heavy abrasion, and operate reliably in extreme temperatures, ensuring the continuous and efficient operation of complex machinery. Even the infrastructure of telecommunications relies on custom cable assemblies for high-speed data transmission, maintaining signal clarity, and ensuring the long-term durability of connections within networking and telecommunications systems, often in challenging outdoor environments. Interestingly, the benefits of custom cables can extend even to seemingly simpler applications, such as creating a clean and optimized setup for a home theater system. In all these scenarios, when the application has specific or demanding requirements, standard off-the-shelf cables often fall short, making custom solutions essential for ensuring optimal performance, safety, and longevity.
Small Batch or Big Order? How Quantity Affects Your Cable Choice.
The decision between choosing a custom cable assembly and an off-the-shelf option can also be influenced by the quantity of cables needed for a project. Generally, for smaller quantities and applications with standard requirements, off-the-shelf cables tend to be more economical due to the lower per-unit cost associated with mass production. However, custom cable assemblies often involve initial design and setup costs, which can make them a less cost-effective choice for very small orders. On the other hand, for larger production runs or when the specific requirements are critical to the performance or safety of the application, the long-term advantages of custom cables can become more compelling. The reduced waste, improved performance, fewer potential failures, and the guarantee of a perfect fit can ultimately lead to overall cost savings that outweigh the initial higher investment. Furthermore, with custom cables, you can order the exact quantity needed, eliminating the issue of having surplus or unusable cables, which can sometimes occur when purchasing standard lengths off-the-shelf. The practicality of choosing custom cable assemblies for different quantities often hinges on the complexity of the requirements. Even a small number of highly specialized cables might necessitate a custom solution, while a large order of standard cables is likely more economically handled with off-the-shelf options. For Original Equipment Manufacturers (OEMs) involved in mass production, custom pre-terminated cable assemblies can significantly streamline the assembly process and minimize the risk of errors, making them a practical choice even for large volumes, despite a potentially higher per-unit cost compared to buying bulk cable and assembling in-house.
Think of It Like This: Easy-to-Understand Analogies.
To better grasp the difference and benefits, consider these analogies:
Imagine buying a suit. You could opt for an off-the-rack suit. It’s readily available and generally less expensive upfront. However, it might not fit you perfectly, and the fabric might not be ideal for all weather conditions or occasions. On the other hand, a tailor-made suit is measured and designed specifically for your body, made from the exact fabric you choose, and tailored to your precise needs, resulting in a much better fit, greater comfort, and enhanced durability. Custom cable assemblies are like that tailor-made suit for your electronics.
Another analogy is software. You could use a generic, off-the-shelf software program for a common task. It might have many features you don’t need, and it might not integrate seamlessly with your other systems. Custom software, however, is developed specifically for your unique workflows and requirements, ensuring optimal performance and seamless integration. Similarly, custom cable assemblies are designed to work perfectly with your specific equipment and system, without unnecessary extras or compatibility issues.
Finally, think about kitchen cabinets. Standard cabinets might fit into your kitchen space, but they might not maximize your storage, match your exact style, or be made of the most durable materials for your needs. Custom-built cabinets are designed to fit your space perfectly, offer optimized storage solutions, and are made from materials that suit your lifestyle and usage. Custom cable assemblies offer the same level of tailored design and material selection for your electronic systems.
Conclusion
In the realm of electronic connections, both off-the-shelf and custom cable assemblies have their place. Off-the-shelf options provide a convenient and cost-effective solution for many standard connectivity needs. However, when your project demands a precise fit, optimized performance, and enhanced durability in specific or challenging environments, custom cable assemblies offer a tailored solution that can ultimately lead to greater efficiency, reliability, and long-term cost savings. The decision ultimately comes down to the specific requirements of your application. When faced with cable choices, remember to consider the unique demands of your project. Sometimes, going custom is the key to a perfect connection.
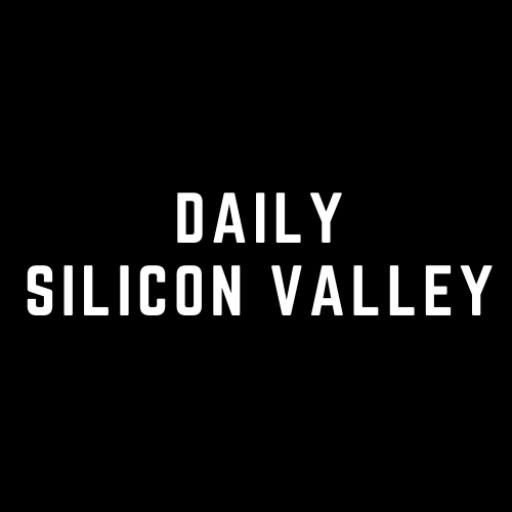
Daily magazine for entrepreneurs and business owners